(21)
以上两式代入(7)(11)(15)整理得到:
(22)

(23)
将分离效率函数(23)式代入组分物料衡算方程,化简可得:

(24)
上式可表示成三对角矩阵的形式,用追赶法求解可得到全塔的气相组成。
方程(1)(10)整理得到气相流量的计算式:
(25)
4.2模拟计算条件
利用非平衡级模型对某炼油厂的酯交换法生产碳酸二甲酯的反应精馏过程进行了模拟计算。该塔有120层直径为0.8米的塔板,操作过程中只有两股进料,无气液相侧线采出。碳酸丙烯酯在27层塔板进料,进料流量为18.2Kmol/h;甲醇在94层塔板进料,进料流量为153.5Kmol/h;甲醇钠从塔的顶部加入,浓度为0.5wt%。塔顶采出量为93.20Kmol/h,回流比为13.5核心期刊目录。
4.3模拟计算步骤

图2 计算框图
通过设定各层塔板上的气液流量、组成及温度的初值,将方程组线性化;采用迭代法求解各组分的物料平衡方程校正气相组成;通过分离效率函数求解液相主体和相界面处的液相组成;然后用焓衡算方程求解气液相流量。见计算框图2。
4.4模拟计算结果
由于生产现场只能提供塔顶冷凝器和塔底再沸器有关数据。由表3与表4可见模拟结果与实测数据比较接近。塔内各组分浓度分布如图3所示。
表3冷凝器液相摩尔组成
计算结果与实测数据的比较
组 分 实测值 模拟值
|
甲 醇 0.8247 0.8239
碳酸丙烯酯 0.0064 0.0059
碳酸二甲酯 0.1607 0.1614
丙二醇 0.0082 0.0088
|
表4 再沸器液相摩尔组成
计算结果与实测数据的比较
组 分 实测值 模拟值
|
甲 醇 0.7482 0.7479
碳酸丙烯酯 0.0798 0.0826
碳酸二甲酯 0.0031 0.0000
丙二醇 0.1689 0.1695
|
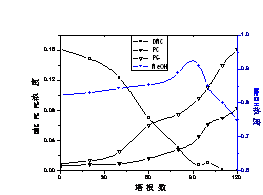
图3各组分浓度分布图
5.优化计算
在反应精馏过程准确模拟的基础上,考察进料比、塔顶采出和回流比三因素对生产过程的影响,建立反应转化率的优化经验模型:

 
(26)
采用均匀设计法模拟实验选取25个操作点,计算相应的转化率,并将其进行多元线性回归,得到优化模型方程。用网格法进行优化计算,得到最优操作条件:塔顶采出量为92.628Kmol/h、回流比为11.86、进料比为15.96,反应转化率可以达到99.99%,与优化前相比提高了3.13%。
6.结论
(1)在计算过程中引入分离效率函数并且假设塔板上气液相达到热量平衡是切实可行的,使计算过程大为简化。
(2)模拟计算方法适用于该体系反应精馏工艺过程非平衡级模型,模拟计算结果与实测数据吻合良好,为仿真软件的开发奠定了基础。
(3)建立的反应转化率的优化经验模型是合理的,对工业生产具有一定的指导意义。
符号说明
c-总组分数
C-组分浓度,mol/l
DMC-碳酸二甲酯
f-反应转化率
F-进料流率,mol/s
H-组分摩尔焓,KJ/mol
i-组分数
j-级数
K-相平衡常数
k-传质系数,mol/m2s
L-液相流率,mol/s
ME-甲醇
N-总分离级数
为某反应物的转化量
PC-碳酸丙烯酯
PG-丙二醇
Q-级上热量 KJ/s
r-反应速率,mol/l min
R-反应量, mol/s
S-侧线采出流率,mol/s
T-温度,K
V-气相流率,mol/s
x-液相摩尔组成
y-气相摩尔组成
-化学计量系数
-分离效率函数中的系数
为反应转化率
上角标
F-进料
I-界面
L-液相
r-反应
V-气相
下角标
0-为某反应物的初始量
i-组分数
j-级数
+-正反应
--逆反应
参考文献:
[1]刘宗健.酯交换法合成碳酸二甲酯研究进展[J].浙江化工,1999,30(2):18-21.
[2]张少钢.碳酸二甲酯合成反应的工艺条件及动力学研究[J].化学反应工程与工艺,1991,
7(1):10-19.
2/2 首页 上一页 1 2 |