图5为不同工况实测缸盖表面振动速度、缸内压力曲线及由此计算得到的压升率曲线的对比结果。由图可见,燃烧开始后,实测振动速度和压力升高率有相似的变化趋势,这表明振动速度信号主要包含燃烧激励相关的信息。同时也可看出,由于约束支架自身振动的存在,使得燃烧始点处振动速度具有一定的初始值,且不同转速下该初始值不同,如1000r/min工况,燃烧始点处振动速度初值约为42.07mm/s,而1400r/min工况约为1.87mm/s。由此导致燃烧始点前振动速度的变化趋势不同,这使得直接利用振动速度识别燃烧始点及最大压力升高率存在一定困难。
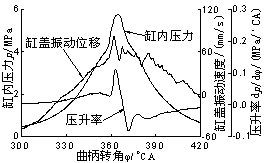
(a)1000r/min工况

(b)1400r/min工况
图5振动速度、缸内压力及压升率对比曲线
采用前面处理振动位移信号的分析方法,将振动位移信号中叠加的低频成分作为趋势项进行处理,通过对比选取适当的多项式拟合得到振动位移信号中叠加的趋势项,并将其从实测振动速度信号中去除,最终得到主要包含缸内燃烧激励信息的振动速度信号,去除趋势项后的振动速度信号见图6。
包含缸内燃烧状态主要特征参数的频率成分在300~2000Hz频带内,为此,基于窗口法设计了通带为300~2000Hz的FIR带通滤波器,用于对实测振动速度信号进行滤波处理,处理后的信号见图6。由图可见,采用去除趋势项的方法及滤波方法得到的振动速度信号具有相近的变化趋势,该趋势与压升率的变化趋势相近,而且处理后的振动速度信号与压升率中包含的关键折点,如燃烧起始时刻点、最大压升率位置等出现的时刻接近,可以从中提取燃烧相关的信息。

(a)1000r/min工况

(b)1400r/min工况
图6处理后振动速度与缸内压力及压升率对比曲线
4缸盖振动加速度分析
振动加速度是振动速度的导数,对高频信息敏感,约束支架低频振动对加速度信号的影响会进一步削弱。图7为两工况振动加速度、缸内压力及其二阶导数对比曲线。由图可见,振动加速度信号中仍叠加了约束支架引起的低频振动,但振动幅值远小于其他激励产生的的加速度振动幅值,由此认为系统自由振动对加速度信号的影响可以忽略。由图中还可看出,循环内除燃烧激励外,振动加速度信号中还存在其他激励源的振动响应信号,根据响应信号出现的相位,认为这些响应信号多由进、排气门开启及关闭撞击激励产生,由于撞击激励多为高频成分,故容易被振动加速度传感器测得。

(a)1000r/min工况
(b)1400r/min工况
图7振动速度、缸内压力及其二次导数对比曲线
对实测1000r/min工况的缸内压力及其二次导数进行了频谱分析,结果见图8,由图可见,研究用机型的缸内压力二次导数频谱能量主要集中在2kHz以下的频段内,对其他多个机型的缸内压力二次导数进行频谱分析,发现频带能量多集中在2kHz以下的频段内。试验中振动加速度传感器布置在缸盖上,测点同燃烧激励间无大阻尼结构;而且缸盖、机体系统的刚度大,测点的变形相对于系统的物理尺度小,可将整个系统简化为线性系统。对线性系统而言,激励源的频谱成分同响应信号的频谱成分是一一对应的,即与缸内燃烧过程密切相关的振动加速度信号的频率成分主要分布在2kHz以下的频段。设计了截止频率为2kHz的低通滤波器对测得的振动加速度信号进行滤波处理。

图8缸内压力及其二次导数频谱分析结果
图9显示了两工况时,低通滤波处理后的振动加速度及缸内压力二次导数的对比曲线。由图可见,两信号在燃烧主要阶段的变化趋势相近,振动加速度信号中包含了较多燃烧相关的信息,可以用于提取缸内燃烧特征参数。从前面图7中可以看出,缸盖振动加速度对低频的约束支架振动不敏感,但对气门系的撞击激励等产生的高频成分敏感,尤其是随着缸数的增加,各激励源出现的时刻接近,研究中在2缸、4缸、6缸及12缸柴油机上进行了实验,通过对实测的缸盖振动加速度信号进行分析,发现上述各机型的缸盖振动加速度信号中都包含了丰富的燃烧相关信息,可以用于对缸内燃烧状况进行分析。由于实验条件所限,未进行更多缸数柴油机的实验,通过已进行的实验,认为对于常用的车用柴油机而言,可以利用振动加速度信号反映缸内燃烧状况。

(a)1000r/min工况

图9滤波后振动加速度及缸内压力二次导数对比曲线
5结论
1.柴油机约束支架振动对缸盖振动位移信号有较大的影响,从缸盖振动位移信号中提取缸内燃烧特征参数较为困难
2.缸盖振动速度信号受柴油机约束支架振动影响小,通过采用去除趋势项或滤波的方法,可以得到含有丰富燃烧相关信息的成分,用于反映缸内燃烧状况
3.缸盖振动加速度信号对高频成分敏感,约束支架对其影响基本可以忽略,通过对常用机型的实验分析认为,可以用于反映缸内燃烧状况。 2/3 首页 上一页 1 2 3 下一页 尾页 |