摘要本文阐述了采用CAE技术分析某壁厚不均匀塑件的成型过程,并根据分析报告详细寻找产生成型质量问题的原因,结果表明,浇口位置的选择对壁厚不均匀塑件的成型质量影响非常大。并通过CAE技术,找出了一个理想的浇口位置,解决了原始方案存在的各种成型质量问题。本文还结合案例和相关理论知识,提出了小型壁厚不均匀塑件的浇口位置确定的原则。
论文关键词:壁厚不均匀塑件,CAE技术,浇口位置,熔接痕,气穴
在注塑模设计过程中,浇口位置的选择关系到塑料熔体在型腔内的压力分布、冷却补缩,以及产品外观质量甚至产品的力学强度,是注塑模设计成功的基础。对于壁厚不均匀的塑件而言,很难通过直观分析而获知熔体在型腔内的充填、冷却状态。有了注射模CAE技术后,可以将计算机技术、塑料流变学和弹性力学有机地结合在一起,利用计算机的高速存储和运算能力,将塑料熔体的充填、冷却过程动态的显示出来,实现了短时间内对各种设计方案进行准确的比较和评测。有了CAE技术作支撑,结合相关的理论知识,可以有效的解决壁厚不均匀塑件浇口位置确定难的问题[1~4]。
以下是某镀铬外盖塑料产品(以下称亮铬盖)在生产中遇到的问题,以及采用CAE技术分析解决问题的过程。
2 问题描述及原因分析
2.1 塑件及初始方案问题描述
亮铬盖产品尺寸最宽处约40mm,总长约120mm,塑件主体壁厚为2mm,边缘壁厚为5mm左右围绕成一个环行的圈,端部薄壁处壁厚为1.5mm,fig.1所示。
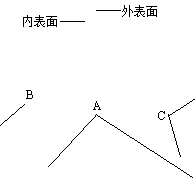


A—壁厚2mm B—壁厚5mm C—壁厚1.5mm
Fig.1 three-dimensional figure of product
该产品为电镀件,成型所用材料为可电镀ABS塑料,熔体流动性一般,考虑到塑料熔体在型腔内的流长和保压问题,将浇口位置放在了塑件的中部,由于塑件是电镀外观件,所以采用了潜伏式浇口,如fig.2所示为划分好网格的塑件浇注系统原始方案:

图2 划分好网格的浇注系统方案
Fig.2 the runner system at the generated mesh
该浇注系统方案从理论上分析无明显的缺陷,于是按照该方案制造了模具,但在注塑成型过程中,塑件的大端从内孔一直延伸到外边缘,出现了一条较为明显的痕迹。而在塑件小端塑件壁厚的过渡区,也出现了流动痕迹,并且经过电镀处理后,这两条痕迹无法完全遮蔽。
2.2 成型质量问题原因分析
观察上述塑件结构,其主体部分在中间,其壁厚为2mm,而其边缘壁厚达到5mm,塑料熔体在进入模具型腔后,很容易形成“跑道效应”,也就是说熔体将先沿充填阻力小的边缘流动,而在中间壁厚较小的位置充填速度较小,这就导致模腔内的部分空气无法“逃逸”。被压缩在型腔中心的空气会沿塑料熔体前沿相交位置分布,形成无法通过模具温度或熔体温度调节而改善的熔接痕;而塑件的壁厚不均匀,使熔料在型腔中的流速产生变化,当从厚壁进入薄壁时,塑料熔体还会出现滞流,形成滞流痕。由于塑件为壁厚不均件,熔体在型腔中的充填速度不均匀,采用经验分析无法准确的确定熔体流动前沿,故借助CAE软件分析问题产生的原因。分析采用软件系统材料库中的ABS Generic Estimates作为分析替代材料,注塑条件选取默认,fig.3为模拟分析结果示意图。
a. fill time

b. weld lines and air traps

c. orientation

d. temperature at flow front
图3 初始方案的流动分析结果
fig.3 the flow analysis results of primary case
从fig.3a熔体充填的时间等位线可以看到,塑料熔体沿壁厚较厚的边缘快速充填,从两个方向在图中A位置形成对接形式的熔接线,导致熔料的熔接效果差。而从fig.3b熔接线及气穴位置图,可以清楚的看到,在前沿熔料熔接时,有大量的空气被挤压积聚在此处无法排出,fig.3c是熔体流动分子取向图,从该图进一步的印证了熔接线形成及空气被积聚的原因。Fig.3d反映了熔体前沿温度的情况,对于本案例大小的塑件,模具结构合理、工艺参数适当,熔体前沿的温度很容易控制在2~3℃范围内;而该塑件由于熔体流动前沿压缩空气的存在,致使熔体充填阻力增大,流动速度变缓,熔体前沿温度也出现了急剧下降,滞流区的温度普遍下降了20℃左右,这是一个流动充填极差的案例。因此,熔体前沿以对接的形式熔接、熔接线位置存在大量压缩空气以及熔接区域出现巨大的温度降低,这三个原因同时存在,出现连电镀都无法遮蔽的熔接痕就不难理解了。
另外,从fig.3a和fig.3d可以清楚的看到,在B处熔体出现滞流,并且也伴随着巨大的熔体前沿温度降低,从而导致塑件在该位置出现明显的滞流痕。
3 较为合理的解决方案
3.1 合理的方案描述
要解决熔接痕对接、排气以及熔体滞流等问题,对于单一浇口注塑模而言,必须通过改变浇口位置来实现。本文塑件的厚度不均匀,由于要考虑补缩问题而将浇口开设在了壁后处,出现了本文上面描述的的成型质量问题;但如果考虑将浇口开设在薄壁位置,又会担心熔体在壁厚较大的位置处补缩困难的问题。有了CAE技术的支撑,可以几乎零成本尝试各种浇口位置设置方案,从而减少不必要的经济损失。经过多个浇口位置的尝试,获得较为理想的浇口位置,fig.4所示为该方案的浇注系统布局情况,此方案将浇口位置开设在壁厚最薄的小端,采用端部侧浇口进料的方式。

图4 浇注系统改进方案
fig.4 the runner system of modified case
3.2 调整后的方案分析
方案改进后,浇注系统的流道变长了,充填压力降势必会有所增大,但若充填压力增大的值在合理范围内,而又能将原始方案中的问题从根本上加以解决,则这种方案的改进就是可取的。图5所示为方案改进后的模拟分析结果示意图。
a. fill time

b. weld lines and air traps
c. temperature at flow front
图5 改进方案模拟充填分析结果
fig.5 the flow analysis results of primary case
从fig.5a可以看到,熔体在型腔中的充填速度非常均匀,壁厚最薄处由于处于进浇位置,所以没有出现滞留现象;而熔体的最后充填区域刚好位于塑件顶部内孔的位置,型腔内被流动前沿“驱赶”积聚的压缩空气可以沿型芯与模板连接的缝隙被导出,所以不会形成熔接痕也不会存在气穴。
1/2 1 2 下一页 尾页 |